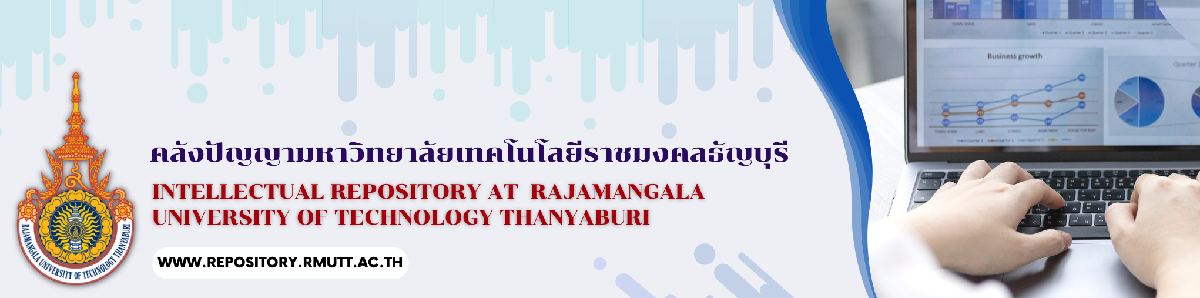
Please use this identifier to cite or link to this item:
http://www.repository.rmutt.ac.th/xmlui/handle/123456789/1134
Title: | การปรับปรุงคุณภาพกระบวนการฉีดพลาสติกด้วยเทคนิคซิกส์ ซิกม่า : กรณีศึกษา บริษัท โคคูโย-ไอเค (ประเทศไทย) จำกัด |
Other Titles: | Process Improvement of Plastics Injection Using Six Sigma Technique: Case Study of KOKUYO-IK (Thailand) Co., Ltd. |
Authors: | สมยศ วงษ์น้อย |
Keywords: | การควบคุมกระบวนการผลิต ซิกส์ ซิกม่า (มาตรฐานควบคุมคุณภาพ) |
Issue Date: | 2555 |
Publisher: | มหาวิทยาลัยเทคโนโลยีราชมงคลธัญบุรี. คณะบริหารธุรกิจ |
Abstract: | การศึกษานี้มีวัตถุประสงค์เพื่อแก้ไขปัญหาจุดดา (Black Dot) และปัญหาการฉีดไม่เต็ม (Short) ของกระบวนการฉีดพลาสติก โดยการประยุกต์ใช้หลักการบริหารคุณภาพตามแนวทางซิกซ์ ซิกม่า จากข้อมูลในอดีตพบว่า ปัญหาฉีดชิ้นงานเสียอยู่ที่ ร้อยละ 0.86 (8,622 PPM) รวมไปถึงข้อร้องเรียนภายในและภายนอกรวมกันเฉลี่ยอยู่ที่ 2.5 ข้อร้องเรียนต่อเดือน ขั้นตอนการดาเนินการวิจัยประกอบด้วย 5 ขั้นตอนตามหลักการของ Six Sigma คือ 1.กำหนดปัจจัยสำคัญที่มีผลกระทบต่อกระบวนการฉีดพลาสติก 2.เก็บข้อมูลเพื่อนามาประเมินและวัดผลก่อนการปรับปรุง 3.วิเคราะห์หาสาเหตุที่เกิดขึ้นของแต่ละปัจจัยหลักที่ส่งผลกระทบต่อกระบวนการฉีดพลาสติกมากที่สุด 4.นำเฉพาะปัจจัยและปัญหาหลักที่ส่งผลกระทบต่อกระบวนการฉีดพลาสติกมาแก้ไข ปรับปรุง 5.ตรวจสอบและควบคุมขั้นตอนการปฏิบัติงานของพนักงานผู้เกี่ยวข้องให้เป็นไปตามคู่มือ และมาตรฐานที่กำหนดอย่างเคร่งครัด ขั้นตอนการวิเคราะห์ปัญหาและสาเหตุของปัญหาใน 6 กระบวนย่อยคือ ขั้นตอนการล้างวัตถุดิบที่ค้างอยู่ ขั้นตอนการฉีดงาน (Injection) ขั้นตอนการตรวจสอบงาน ขั้นตอนการล้างหม้ออบ ขั้นตอนการตรวจสอบวัตถุดิบและขั้นตอนการนาแม่พิมพ์ลงพร้อมบำรุงรักษาก่อนจัดเก็บ จากนั้นทำการวิเคราะห์ระบบการวัดและประเมินความสามารถของกระบวนการรวมถึงการวิเคราะห์หาสาเหตุที่แท้จริง แล้วทาการปรับปรุงโดยใช้การออกแบบการทดลองขั้นตอน สุดท้ายคือ นาแนวทางหรือวิธีการที่ดีที่สุดไปควบคุมในขั้นตอนการปฏิบัติงาน ผลที่ได้หลังจากทำการปรับปรุงสามารถลดปริมาณชิ้นงานบกพร่องโดยสามารถแก้ 2 ปัญหาใหญ่ซึ่งก็คือ ปัญหาชิ้นงานมีจุดดำ และปัญหาฉีดงานไม่เต็มจากเดิมปริมาณของเสียอยู่ที่ ร้อยละ 0.86 (8,622 PPM) หลังการปรับปรุงลดลงมาอยู่ที่ ร้อยละ 0.59 (5,900 PPM) และจะสามารถลดข้อร้องเรียนจาก 2.5 ข้อร้องเรียนต่อเดือนลดลงเหลือ 1 ข้อร้องเรียนต่อเดือน The purposes of this study were to solve black dot and short defect problems of the plastics injection process by adopting Six Sigma technique which was one of the quality management techniques. From the historical data, the plastic injection defects were 0.86% which was about 8,622 PPM, and the internal and external complaints were 2.5 complaints per month on average. The research procedure used Six Sigma technique which consisted of 5 phases as follows: Define the problem that affected plastic injection process, Measure by collecting and evaluating the relevant data before improvement process, Analyze by seeking out root cause of each factor that most affected plastic injection process, Improve or optimize factors and main causes that affected plastic injection process, and Control the operational process to strictly follow the manuals and standards. The analysis phase found that causes and problems of 6 sub processes were purging the remaining material, injecting, checking, cleaning the hopper, and investigating raw material and maintaining mold before keeping. The measurement and performance evaluation systems were analyzed to find the root cause and design the experiments to improve. The final phase was using the optimization to control the operational process. The results after improvement were able to reduce defects by solving 2 main problems, which were black dot and short defect problems. Before improvement, defects were 0.86% which was equal to 8,622 PPM, and there were 2.5 complaints per month on average. After improvement, the defects were reduced to 0.59% which was equal to 5,900 PPM, and the complaints were reduced to 1 complaint per month on average. |
URI: | http://www.repository.rmutt.ac.th/dspace/handle/123456789/1134 |
Appears in Collections: | การค้นคว้าอิสระ (Independent Study - BUS) |
Files in This Item:
File | Description | Size | Format | |
---|---|---|---|---|
132437.pdf | 5.09 MB | Adobe PDF | View/Open |
Items in DSpace are protected by copyright, with all rights reserved, unless otherwise indicated.